Technische Trainings
Die German Centre Taicang Academy bietet folgende Technische Trainings an.
Date: | May 21st-22th (Taicang) June 26th-27th (Shanghai) |
9:00 am – 5:00 pm | |
Venue: | German Centre Taicang/Shanghai |
Language: | Chinese |
Price: | Standard Price: 6,500 RMB Early Bird Price: 5,880 RMB Group Price: 5,680 RMB |
Course Introduction
In order to improve production efficiency and address the challenges of recruiting post-90s and post-00s workers, seasonal labor shortages, and rising labor costs, many enterprises are increasingly turning to automated production lines and robotic equipment. This not only significantly enhances production efficiency but also alleviates labor shortages.
However, this has also brought about unprecedented safety risks. Traditional manual production lines, although less efficient, have lower safety risks. In contrast, automated production lines and robotic equipment, despite their high efficiency, carry exponentially higher safety risks. Any issues in equipment design, manufacturing, installation and commissioning, operation, or maintenance can easily lead to casualties. An example of this is the fatal accident at the Shanghai Tesla Gigafactory in 2023.
Safety regulations for machinery vary globally, resulting in different safety levels for the same equipment in different countries. In China, many national mechanical safety standards marked with „GB/Txxx“ are recommended standards, but in reality, they must be strictly implemented. Equipment manufacturers, driven by profit, often conceal this from customers and shift the risks, endangering employees‘ lives and increasing the compensation costs for enterprises.
Currently, most customers have outdated knowledge about the safety of automated production lines, with prominent issues such as: 90% of customers lack an understanding of the management methods for the entire safety life cycle of machinery; 90% of suppliers have insufficient design capabilities to ensure equipment safety, and customers are unable to conduct proper acceptance checks while remaining overconfident; enterprises have not established internal mechanical safety management systems, making it difficult to control the entire process; there is poor communication between both parties, lacking implementation standards; customers have no criteria for selecting suppliers, leading to cooperation with inferior ones, and their own teams are reluctant to improve; both parties have a shallow understanding of safety standards, being unable to conduct risk assessments or establish safety loops, making accidents highly likely.
This course directly addresses these pain points, providing systematic solutions to help enterprises establish a mechanical safety management process, control the essential safety throughout the life cycle, and safeguard against accidents while improving safety performance.
Target Audience:
Management and technical teams, including plant managers, production/process/maintenance/EHS managers, supply chain personnel, engineers, and technicians from equipment manufacturers.
Training Objectives:
- Establish full life-cycle inherent safety management for machinery & robotics, covering SDR/SAT/FAT phases.
- Master machinery safety risk assessment (ISO 12100.1 & ISO 13849.1) and tools to design compliant safety control loops (PL ≥ PLr).
- Understand global machine safety regulations and strategies to mitigate risks.
- Analyze root causes of robotic accidents and unsafe maintenance practices (e.g., bypassing safety systems).
- Explore smart LOTO solutions and vision-based safety technologies for robotics.
Course Outline
Chapter 1: Fundamentals of Machinery Safety
1. Mechanical motions and operations
2. Types of mechanical hazards
3. Hazardous zones in machinery
4. Safety protection methods
4.1 Types of guards
4.2 Guard design requirements
4.3 Safety device categories
5. International and Chinese safety standards (ISO/IEC/GB)
6. Safety distance calculations
6.1 Safety fences
6.2 Light curtains
6.3 Two-hand controls
6.4 Safety mats
7. Accident prevention
7.1 Hierarchy of risk reduction
7.2 Protective measures
Chapter 2: Risk Assessment and Safety Loop Design
1. Risk assessment methodology
1.1 Machine limits
1.2 Hazard identification
1.3 Risk estimation (S/F/P)
1.4 Risk evaluation
2. Risk reduction principles
2.1 Inherent safety design
2.2 Protective measures
2.3 Complementary measures
2.4 Residual risk communication
3. Safety design requirements
3.1 PL vs. PLr
3.2 PL determination
3.3 PL calculation
3.4 Key parameters for PL
3.5 Evaluation steps
3.6 Category definitions (B/1/2/3/4)
3.7 MTTFD calculation
3.8 DCavg and CCF validation
3.9 PL calculation case studies
Chapter 3: Life-cycle Safety Management
3.1 Safety considerations in SDR phase
3.2 SAT safety requirements
3.3 FAT acceptance criteria
3.4 Operational safety management
Chapter 4: Robotic Safety
1. Common robotic accident analysis
2. Maintenance risks and safety bypass practices
3. Smart locks, LOTO systems, and vision-based safety solutions
4. Safety products for robotic applications
Instructor profile
Du Chenglong, with 25 years of EHS and sustainability experience, has held engineer and senior management roles in six multinational corporations. As former China/APAC EHS Head at a Swedish multinational, he led teams to resolve safety issues across 1,000+ machines with high risk and completed 50+ hours of advanced machinery safety engineer training.
About Lvda Anheng
Suzhou Lvda Anheng Safety and Environmental Protection Technology Co., Ltd. was founded in Taicang City in August 2016, focusing on providing customers with technical consulting services in Environmental, Health and Safety (EHS). The company has been put on record with the Emergency Management Bureaus of Suzhou, Taicang and Kunshan. It has a professional team with an average working experience of over 10 years. The team members include senior engineers, national certified safety engineers, as well as experts from the emergency management bureaus of Taicang, Suzhou and Shanghai, demonstrating strong professional capabilities. Currently, the company’s business covers all districts and counties of Suzhou and Shanghai. By virtue of its professional services, it has won the trust of numerous customers and built a solid safety and environmental protection barrier for regional development.
Date: | July 30th – 31st (Taicang) August 28th–29th (Shanghai) |
Time: | 2-day training (9:00 AM–5:00 PM daily) |
Venue: | German Centre Taicang/Shanghai |
Language: | Chinese |
Price: | Standard Price: 6,500 RMB Early Bird Price: 5,880 RMB Group Price: 5,680 RMB |
Course Introduction
Many corporate managers face a perplexing issue: despite declining injury rates and fewer identified hazards, severe accidents causing serious injuries or fatalities still occur unexpectedly. Such incidents erode confidence in safety management, casting doubt on the belief that “all accidents are preventable.”
In reality, most safety professionals and managers understand that “safety management is risk management.” However, misconceptions about risk persist. A key example is the distinction between risks leading to Serious Injury or Fatality (SIF) and those causing minor injuries. SIF-related risks are characterized by “high consequence, low frequency,” while minor injuries typically stem from “low consequence, relatively higher frequency” risks. Low-frequency risks often lead to cognitive biases, such as neglect or selective ignorance, particularly when hidden unsafe behaviors become normalized among employees. Without understanding daily operations, managers may fail to identify and correct these behaviors, delaying risk mitigation.
To control SIFs, it is critical to build a preventive safety management system, measure its effectiveness and maturity, and eliminate or reduce Potential SIF (PSIF) events. This includes establishing safety observations, audits, and continuous PSIF reduction strategies. Examples from industry practices include:
1. SIF Prevention in Manufacturing
A manufacturing company successfully reduced SIF incidents by 40% within six months through:
- Employee safety observation systems.
- Monthly safety training for all staff.
- Data analytics to predict high-risk zones.
2. Cumulative Risk Management in Construction
A construction company implemented cumulative risk analysis for high-altitude work:
- Identifying risks early in projects.
- Calculating cumulative risk indices (weather, worker experience, equipment status).
- Halting work when indices exceeded safety thresholds.
This course systematically explains how to manage 21% of SIF/PSIF risks in manufacturing industry through 360° strategies.
Target Audience:
GM,plant managers, department heads and EHS professionals (managers, supervisors, engineers).
Training Objectives:
This course addresses the following challenges:
- Understanding SIF/PSIF and managing 21% of high-risk operations.
- Establishing proactive metrics (e.g., PSIF event counts, safety observation coverage, leadership engagement).
- Building a PSIF/SIF near-miss matrix and behavioral observation systems.
- Designing a **SIF/PSIF Risk Control System** to measure maturity, including:
- Evaluating current safety performance and identifying improvement steps.
- Transitioning from reactive (“compliance-driven”) to proactive (“risk elimination”) safety cultures.
- Covering **11 themes and 51 modules** (e.g., lockout/tagout, mechanical safety, contractor management).
- Leveraging AI cameras and big data to capture high-risk behaviors and analyze root causes.
Course Outline
Prologue: SIF and PSIF
- Limitations of the Classic Heinrich’s Theory and Applications of the Updated Version
- How the Revised Heinrich’s Theory Addresses SIF Prevention and Management
- Definitions of SIF/PSIF
- Strategies to Prevent SIF Occurrences
- Integrating SIF (Reactive Metrics) and PSIF (Proactive Metrics) into Safety Indicator Systems
- Understanding PSIF Events
- PSIF/SIF Near-Miss Matrix and Behavioral Safety Observations
- Criteria for Identifying SIF/PSIF and Exposure to Nine High-Risk Operations
- Management Requirements for Nine High-Risk Operations and Measuring Corporate Safety Management Maturity
Chapter 1: Safety Management System Requirements
- Organizational Methods & Health/Safety Planning
- Visible Safety Leadership
- Risk Assessment Management
- Incident & Event Management
Chapter 2: Change Management
- Change Management Process
- Stakeholder Involvement
- Change Authorization
- Change Communication
- Change Impact Assessment
Chapter 3: Transportation, Storage & Logistics Safety
- Transportation Planning
- Training & Certification
- Safe Loading/Unloading Practices
- Intrinsic Safety Requirements for Vehicles (e.g., Forklifts)
- Racking Safety Standards
- Aisle and Floor Safety Requirements
- Pedestrian and Walkway Safety
- Safe Driving Protocols
Chapter 4: Lifting Operations and Crane Safety
- Lifting and Securing Techniques
- Crane Safety Technologies
Chapter 5: Fall Prevention
- General Requirements for Fall Protection
- Management of Elevated Work Equipment
- Training and Permitting
- Compliance Documentation
Chapter 6: Personal Protective Equipment (PPE)
- Risk Assessment (Walk-Through Evaluations)
- PPE Selection Criteria
- Specific PPE Management
- Employee Training & Recordkeeping
Chapter 7: Industrial Hygiene Hazard Exposure
- Procedures, Work Instructions, and Training
- Evaluation and Archiving
- High-Pressure Gas Cylinder Safety
- Chemical Labeling & Storage
- Noise & Vibration Control
- Ventilation and Emissions Management
- Confined Space Safety
Chapter 8: Mechanical Safety
- Training & Competency Requirements
- Lifecycle Management of Mechanical Safety (SAT/FAT)
- Work Instructions
- Mechanical Risk Assessment Records
- Mechanical Safety Preventive Maintenance (PM)
Chapter 9: Lockout/Tagout (LOTO)
- LOTO Risk Assessment and Task Lists
- LOTO Execution Requirements
- LOTO Equipment Standards
- LOTO Training Programs
Chapter 10: Contractor Safety
- Safety Considerations in Bidding Processes
- Pre-Qualification of Suppliers
- Contractor Training
- Pre-Work Risk Assessments and Safety Plans
- On-Site Safety Supervision
- Post-Work Evaluations
Instructor profile
Du Chenglong has dedicated 25 years to the field of EHS (Environment, Health, Safety) and sustainable development, boasting profound professional experience. He has successively worked for six major foreign-funded enterprises, rising step by step from a grassroots engineer to a senior manager. He rooted himself in a well-known Swedish multinational company for 14 years, serving as the EHS Manager for the Chinese region for 11 years, and later taking on the crucial role of the EHS head for the Asia-Pacific region for 3 years, making substantial contributions to the development of regional businesses.
Moreover, as a senior trainer, Du Chenglong led a team to assist 15 companies in the Chinese region in implementing a specific management system. During this process, he meticulously planned and overcame numerous difficulties, significantly enhancing the management efficiency of each company. As a result, these companies have achieved remarkable accomplishments in the fields of environment, health, safety, and sustainable development, setting an exemplary model for the industry.
About Lvda Anheng
Suzhou Lvda Anheng Safety and Environmental Protection Technology Co., Ltd. was founded in Taicang City in August 2016, focusing on providing customers with technical consulting services in Environmental, Health and Safety (EHS). The company has been put on record with the Emergency Management Bureaus of Suzhou, Taicang and Kunshan. It has a professional team with an average working experience of over 10 years. The team members include senior engineers, national certified safety engineers, as well as experts from the emergency management bureaus of Taicang, Suzhou and Shanghai, demonstrating strong professional capabilities. Currently, the company’s business covers all districts and counties of Suzhou and Shanghai. By virtue of its professional services, it has won the trust of numerous customers and built a solid safety and environmental protection barrier for regional development.
Date: | September 25th–26th (Taicang) October 30th–31st (Shanghai) |
Time: | 2-day training (9:00 AM–5:00 PM daily) |
Venue: | German Centre Taicang/Shanghai |
Language: | Chinese |
Price: | Standard Price: 6,500 RMB Early Bird Price: 5,880 RMB Group Price: 5,680 RMB |
Course Introduction
On February 8 of 2025, under the unified arrangement of the China Securities Regulatory Commission (CSRC), the Shanghai Stock Exchange, Shenzhen Stock Exchange, and Beijing Stock Exchange released the *Guidelines for Listed Company Self-Regulation—Sustainability Reports (Trial Draft for Public Consultation)* and solicited market feedback. These guidelines encourage A-share listed companies to publish sustainability or ESG reports and specify detailed requirements for report frameworks and content. This marks a significant milestone, guiding companies to comprehensively demonstrate their value and promoting ESG development.
ESG reports serve as a primary means for companies to communicate their ESG performance. However, there is no unified global standard for ESG reporting. Requirements vary across domestic and international markets, leading to diverse disclosure practices. Let’s explore:
What is an ESG Report?
An ESG report is a communication tool for companies to disclose their strategies, practices, and impacts in environmental, social, and governance (ESG) dimensions to stakeholders. Similar to financial reports, ESG reports present non-financial performance in areas such as environmental responsibility, social contribution, and corporate governance.
Value of ESG Reports
- Growing ESG Investment: Companies with strong ESG performance gain access to funding, resources, and investor trust.
- Regulatory Compliance: Increasing regulatory mandates make ESG reporting a necessity.
- Supply Chain Influence: Multinational ESG requirements impact procurement decisions; ESG reports help maintain client relationships.
- Stakeholder Expectations: Consumers, communities, and media demand non-financial transparency to build a responsible brand.
- Risk Management and Talent Retention: Strengthen environmental/social risk management, drive sustainability, and attract talent.
International ESG Disclosure Standards
Globally, organizations have developed diverse ESG standards. Key frameworks include:
- CDP(Carbon Disclosure Project)
- GRI Standards (Global Reporting Initiative)
- CDSB Framework (Climate Disclosure Standards Board)
- SASB Standards (Sustainability Accounting Standards Board)
- TCFD Recommendations (Task Force on Climate-related Financial Disclosures)
- OECD Guidelines for Multinational Enterprises
- ISO 26000 (Social Responsibility Guidance)
- IIRC Framework (International Integrated Reporting Council)
- VRF Framework (Value Reporting Foundation)
2023 Updates:
- ESRS (European Sustainability Reporting Standards) under the EU’s CSRD.
- ISSB’s IFRS S1 and S2 (International Sustainability Standards Board).
Domestic ESG Disclosure Standards in China
China’s ESG regulatory framework has evolved through three stages:
- Pre-2008: Voluntary CSR reporting.
- 2008–2015: Mixed voluntary and mandatory disclosure.
- 2015–Present: Enhanced ESG reporting systems under „dual carbon“ goals.
Key Domestic Standards:
- SSE/SZSE Self-Regulatory Guidelines
- CSRC Annual Report Content Guidelines
- HKEX ESG Reporting Guide
- GB/T 36001-2015 (Social Responsibility Reporting Guidelines)
- CASS-CSR4.0 (Chinese Academy of Social Sciences)
- PBOC Environmental Disclosure Guidelines
Domestic ESG Disclosure Requirements
Regulatory bodies such as the China Securities Regulatory Commission (CSRC), stock exchanges, and the Ministry of Ecology and Environment have established specific requirements for ESG disclosure content and accountability topics.
Environmental (E) Requirements
- Environmental Management: Institutional frameworks, implementation, ecological permits, environmental protection taxes, pollution liability insurance, environmental credit evaluations.
- Policies and Goals: Environmental protection objectives, achievements, major incidents (violations, accidents), voluntary agreements with authorities.
- Investments and Technology: Funding for environmental projects, technological innovations, government incentives.
- Monitoring and Compliance: Self-monitoring plans, mandatory clean production audits, waste management, pollution control measures (facility construction/operation).
- Carbon and Resources: Carbon emissions data, decarbonization efforts, energy/water consumption, biodiversity protection.
- Legal Compliance: Environmental violation records, gaps in social responsibility fulfillment, and corrective actions.
Social (S) Requirements
- Social Responsibility Philosophy: Corporate commitment to ethical practices.
- Employee Welfare: Health, safety, benefits, development, turnover rates.
- Stakeholder Rights: Protection of shareholders, creditors, customers, and consumers.
- Supply Chain and Community: Supplier ethics, public relations, social initiatives (poverty alleviation, rural revitalization, charity).
- **Product Safety**: Quality control, major production/safety incidents.
- Compliance: Scientific ethics, operational integrity, gaps in social responsibility reporting.
Governance (G) Requirements
- Corporate Structure: Governance frameworks, impacts of frequent leadership changes, corrective measures for operational deficiencies.
- Shareholder and Board Oversight: Independence of controlling shareholders, board meeting practices, executive profiles.
- Internal Controls: Risk management, internal audit systems, investor relations, profit distribution, equity incentives.
- Subsidiary Management: Oversight of subsidiary operations.
ESG Disclosure Trends Among Chinese Listed Companies
Since the Shenzhen Stock Exchange introduced the *Guidelines for Social Responsibility of Listed Companies* in 2006, A-share companies have published CSR/ESG reports for nearly 17 years. Although ESG reporting started later, disclosure rates have risen significantly.
In 2023, over **1,800 sustainability reports** were published by A-share companies (up from 1,400 in 2022), covering one-third of all listed firms. The recent *Guidelines* are expected to further standardize and enhance report quality.
Target Audience:
Executives and personnel involved in ESG management, including:
- General Managers (GM), Plant Managers (PM), Directors.
- Managers and staff from EHS, finance, compliance, and related departments.
Training Objectives:
- Understand Key ESG Organizations: History and roles of UNGC, UNFCCC, PRI, RBA, FSC, MSC, and others.
- Master Disclosure Standards**:
- Global frameworks (GRI, ISSB, CDP, TCFD, Ecovadis).
- Domestic standards (HKEX ESG Guide, CASS-ESG 5.0).
- Analyze Rating Criteria:
- International agencies (ISS, Moody’s, MSCI, S&P Global, Sustainalytics).
- Domestic agencies (SinoSec, China Chengxin, Miaoying, CUFE Green Finance Institute).
- Explore China’s ESG Landscape: Macro policies, industry-specific opportunities.
- Enhance ESG Performance: Strategies to improve ratings and align with investor expectations.
Course Syllabus
Chapter 1: Introduction to ESG International Organizations & Organizational Principles
1. UNGC (United Nations Global Compact)
2. UNFCCC (United Nations Framework Convention on Climate Change)
3. RBA (Responsible Business Alliance)
4. WHO (World Health Organization)
5. PRI (Principles for Responsible Investment)
6. FSC (Forest Stewardship Council)
7. MSC (Marine Stewardship Council)
Chapter 2: ESG International Disclosure Standards and Case Studies
2.1 SDGs (Sustainable Development Goals) Initiative and Case Studies
2.2 GRI (Global Reporting Initiative) Framework and Case Studies
2.3 CDP (Carbon Disclosure Project) Framework and Case Studies
2.4 SASB & ISSB (Sustainability Accounting Standards Board & International Sustainability Standards Board) Frameworks and Case Studies
2.5 TCFD (Task Force on Climate-related Financial Disclosures) Framework and Case Studies
2.6 Linkages Between TCFD and Other Initiatives
2.7 ECOVADIS Information Disclosure Framework
Chapter 3: ESG Domestic Disclosure Standards and Case Studies
3.1 HKEX (Hong Kong Stock Exchange) ESG Disclosure Rules
3.2 Domestic ESG Disclosure Rules for SSE, SZSE, and BSE (CASS-ESG 5.0)
Chapter 4: Introduction to Mainstream International ESG Rating Agencies & Standards
4.1 ISS (Institutional Shareholder Services)
4.2 Moody’s ESG Solutions
4.3 MSCI ESG Research
4.4 S&P Global ESG Scores
4.5 Sustainalytics
Chapter 5: Introduction to Mainstream Domestic ESG Rating Agencies
5.1 China Securities Index Co., Ltd.
5.2 CCXI (China Chengxin International Credit Rating)
5.3 MioTech
5.4 Green Finance Research Institute, Central University of Finance and Economics
Chapter 6: Analysis of ESG Development in China
6.1 Macro Policy Analysis of ESG in China
6.2 Current Status and Opportunities of ESG Development in Sub-sectors
6.3 ESG Report Review: Ping An of China (Stock Code: 2056552)
Instructor profile
Du Chenglong has dedicated 25 years to the field of EHS (Environment, Health, Safety) and sustainable development, boasting profound professional experience. He has successively worked for six major foreign-funded enterprises, rising step by step from a grassroots engineer to a senior manager. He rooted himself in a well-known Swedish multinational company for 14 years, serving as the EHS Manager for the Chinese region for 11 years, and later taking on the crucial role of the EHS head for the Asia-Pacific region for 3 years, making substantial contributions to the development of regional businesses.
Moreover, as a senior trainer, Du Chenglong led a team to assist 15 companies in the Chinese region in implementing a specific management system. During this process, he meticulously planned and overcame numerous difficulties, significantly enhancing the management efficiency of each company. As a result, these companies have achieved remarkable accomplishments in the fields of environment, health, safety, and sustainable development, setting an exemplary model for the industry.
About Lvda Anheng
Suzhou Lvda Anheng Safety and Environmental Protection Technology Co., Ltd. was founded in Taicang City in August 2016, focusing on providing customers with technical consulting services in Environmental, Health and Safety (EHS). The company has been put on record with the Emergency Management Bureaus of Suzhou, Taicang and Kunshan. It has a professional team with an average working experience of over 10 years. The team members include senior engineers, national certified safety engineers, as well as experts from the emergency management bureaus of Taicang, Suzhou and Shanghai, demonstrating strong professional capabilities. Currently, the company’s business covers all districts and counties of Suzhou and Shanghai. By virtue of its professional services, it has won the trust of numerous customers and built a solid safety and environmental protection barrier for regional development.
Date: | November 25th-26th (Taicang) December 25th-26th (Shanghai) |
Time: | 2-day training (9:00 AM–5:00 PM daily) |
Venue: | German Centre Taicang/Shanghai |
Language: | Chinese |
Price: | Standard Price: 6,500 RMB Early Bird Price: 5,880 RMB Group Price: 5,680 RMB |
Course Introduction
It is widely recognized that the ultimate goal of safety production is marked by „Zero Accidents & Zero Injuries.“ However, achieving this goal is neither effortless nor instantaneous. It requires continuous innovation in mindset, concepts, behaviors, and methodologies, alongside sustained practical efforts.
For large systems such as corporate groups, the priority is to curb major accidents and control the overall accident rate. For smaller systems like individual enterprises, the focus lies in eliminating potential hazards and unsafe behaviors to ensure equipment safety, compliance, and accident-free operations.
While industry-specific characteristics influence safety management approaches, legal requirements for safety objectives remain consistent. Effective safety management must align with organizational needs—practical, feasible, and results-driven.
How can we achieve Zero Accidents & Zero Injuries? By integrating management theory with scientific safety principles, organizations must prioritize risk control, foster a culture of self-discipline and proactive safety, and develop tailored management models. This ensures systematic execution of safety protocols, rigorous implementation, and measurable results.
Amid China’s rapid industrialization and digital transformation, safety challenges persist, characterized by a „Three Highs, Two Lows“ pattern: high accident rates, high major incident frequency, high risks, coupled with low technical capabilities and workforce competency. This course provides actionable solutions to help organizations achieve their safety goals.
Target Audience
Enterprise managers, including GM, plant directors, department heads, and EHS professionals (managers, supervisors, engineers).
Training Objectives
1. Design Preventive Safety Frameworks
Shift from reactive „firefighting“ to proactive risk management. Focus on addressing 20% of high-impact risks with 80% of efforts.
2. Systematic Risk & Hazard Management
Equip participants with theories, tools (e.g., JHA, FMEA), and case studies to eliminate hazards at their root.
3. Zero Injury Campaign Implementation
Detail front-line strategies for workshop team-level zero-injury initiatives to achieve company-wide safety targets.
4. Identify Improvement Opportunities
Evaluate gaps in organizational design, risk management, and front-line practices to drive sustainable safety transformations.
Course Outline
Chapter 1: Organizational Structure and Model Concepts for Achieving Zero Injuries & Zero Accidents
1.1 The Critical Value of Proactive Safety Management in Enterprises
1.2 Analysis of Efficient Safety Organizational Structures and Responsibilities in Multinational Corporations
1.3 Interpreting Organizational Excellence and Corporate Safety Culture Alignment
1.4 Top-Level Design: The Importance of „Perceptible Leadership“ by Management
1.5 Dimensions of Perceptible Leadership (Personal Safety Action Plans & Accountability Systems)
1.6 Implementing a Proactive Safety Management Model with Perceptible Leadership
1.7 Empowering Managers as Primary Accountability Holders for Enterprise Safety
1.8. World-Class Safety Management Evaluation Standards and Criteria
1.9 Clarifying Misconceptions Hindering High-Level Safety Management
1.10 Addressing the Limitations of Heinrich’s Theory: The Management Value of SIF/PSIF Concepts
Chapter 2: Core Safety Management & Risk Theories
2.1 The U.S. Air Force’s „Three Steel Plates“ Case Study
2.2 The „Short Board“ Theory (Weakest Link Principle)
2.3 The Evolution and Application of Risk Management
2.4 Paradigm Shifts in Safety Management Philosophy
2.5 Fundamentals of Production Safety Risk Management
2.6 Characteristics and Root Causes of Accidents
2.7 Risks vs. Hazard Sources
2.8 Relationships Between Safety, Hidden Hazards, Danger Points, and Accidents
2.9 The Critical Role of Hazard Identification
2.10 Reactive vs. Preventive Safety Management Models
Chapter 3: Theories and Methods for Managing Potential Hazards
3.1 Principles of Risk Analysis
3.2 Detailed Analysis of Accident Causation Factors
3.3 Type I vs. Type II Hazard Sources and Their Interdependence
3.4 Case Study: Hazard Identification
3.5 Risk Management Tools (JHA, PHA, FMEA, EAT, FAT, HAZOP)
3.6 Introduction to Job Safety Analysis (JSA)
3.7 Safety Checklist (SCL) Development
3.8 Four Simplified Hazard Identification Tools:
– Multi-Step Planning
– 10-Second Drills
– 6-Dimensional Observation
– Two-Key-Question Method
Chapter 4: Eliminating Risks & Hazards—Keeping Accidents at Bay
4.1 Case Study: The Sunken Ship Incident
4.2 Four Factors Triggering Accidents and Prevention Strategies
4.3 Breaking the „Accident Chain“
4.4 Hazard Control Systems
4.5 Principles of Risk Mitigation
4.6 Processes and Methods for Accident Prevention
4.7 Ensuring Accountability in Safety Practices
4.8 Retrospective Summary: Achieving Zero Accidents
Chapter 5: Team-Level Zero-Accident Implementation Strategies
5.1 Overview of „Zero-Accident Campaigns
5.1.1 The Link Between Corporate Culture and Accident Rates
5.1.2 Aligning Safety Prevention Activities with Organizational Culture
5.1.3 Three Core Principles of Zero-Accident Campaigns
5.1.4 Three Pillars for Driving Zero-Accident Initiatives
5.1.5 Leadership Demonstration of Safety Commitment
5.1.6 Establishing Autonomous Safety Management at the Team Level
5.2 Risk Prediction Training (KYT)
5.2.1 Overview of KYT
5.2.2 Objectives of KYT
5.2.3 Fostering a Zero-Accident & Zero-Injury Safety Culture
5.3 Shisa Kanko (Pointing and Calling)
5.3.1 Effectiveness of Pointing and Calling
5.3.2 Implementation Guidelines
5.3.3 Training Formats for Shisa Kanko
5.3.4 Key Precautions and Best Practices
5.3.5 Four-Stage Methodology for KYT
Instructor profile
Du Chenglong has dedicated 25 years to the field of EHS (Environment, Health, Safety) and sustainable development, boasting profound professional experience. He has successively worked for six major foreign-funded enterprises, rising step by step from a grassroots engineer to a senior manager. He rooted himself in a well-known Swedish multinational company for 14 years, serving as the EHS Manager for the Chinese region for 11 years, and later taking on the crucial role of the EHS head for the Asia-Pacific region for 3 years, making substantial contributions to the development of regional businesses.
Moreover, as a senior trainer, Du Chenglong led a team to assist 15 companies in the Chinese region in implementing a specific management system. During this process, he meticulously planned and overcame numerous difficulties, significantly enhancing the management efficiency of each company. As a result, these companies have achieved remarkable accomplishments in the fields of environment, health, safety, and sustainable development, setting an exemplary model for the industry.
About Lvda Anheng
Suzhou Lvda Anheng Safety and Environmental Protection Technology Co., Ltd. was founded in Taicang City in August 2016, focusing on providing customers with technical consulting services in Environmental, Health and Safety (EHS). The company has been put on record with the Emergency Management Bureaus of Suzhou, Taicang and Kunshan. It has a professional team with an average working experience of over 10 years. The team members include senior engineers, national certified safety engineers, as well as experts from the emergency management bureaus of Taicang, Suzhou and Shanghai, demonstrating strong professional capabilities. Currently, the company’s business covers all districts and counties of Suzhou and Shanghai. By virtue of its professional services, it has won the trust of numerous customers and built a solid safety and environmental protection barrier for regional development.
Date: | Session I 1. November, 6. Dezember Session II 8. November, 13. Dezember Session III 15. November, 20. Dezember |
Time: | 1:30 am – 5:00 pm |
Venue: | Online |
Attendees: | Employees of both Chinese and Foreign enterprises in China |
Language: | Chinese |
Price: | RMB 400 per session, RMB 1,200 for three sessions |
(*) Hinweis: Dieses Training wird nicht direkt vom German Centre Taicang durchgeführt. Der Trainingsanbieter ist für die Organisation und Durchführung dieses Trainings verantwortlich.
Course Introduction
The VDA Quality Management Center (QMC) China Driver License is a certificate-based online course that consists of 3 sessions, each 3 hours. The content is on quality management systems, QM standards, QM methods, QM audits, project management, core tools, recalls and digitalization. The goal is to deliver the base of a “Quality Culture”, to help spread the basic quality knowledge to a broad audience within manufacturing and service companies and educational institutions. These courses support the growing trend to innovative products and processes, as „Innovation helps generate new demands from customers. Quality helps capture the value of our innovation”. In order to bring the “quality first mindset” to everybody’s doorstep, VDA-QMC in cooperation with the VDA license partner Accu X-Tech are pleased to invite you to the online sessions of our comprehensive quality upgrade educational courses.
This course is organized by the German Automobile Manufacturers Association (VDA), which is tailored for the Chinese market. The contents cover: quality management system, QM standards and related methods. The aim is to broaden the knowledge of students and popularize this „quality“ education. After successfully completion and passing the exam, students will obtain the VDA QMC China Driver License certificate jointly issued by Professor Tilman Tillmann, General Manager of VDA Quality Management Center China Branch, and Dr. Wolfgang Wagner.
VDA, or “Verband der Automobilindustrie”, is an association composed of car manufacturers and their partners, suppliers and tractor manufacturers to unify standards of the German auto industry. The VDA standards are extremely important to the automotive industry, some of which are mandatory standards that automotive and parts companies must meet, and almost all companies in the automotive industry have to pass the VDA certification. Due to the status of the German automotive industry in the world, VDA can also be viewed as a representative of an advanced automotive industry standard.
Earlier before, VDA training programs in China catered mainly to senior managers and senior process auditors. This VDA QMC China Driver License training program however is mainly targeting for attendees who are grass-roots managers, such as in the field of production and manufacturing, quality management, development and design, procurement and sales of automobile and automotive parts manufacturing enterprises. Employees in almost all departments of the enterprise may easily gain an understanding of this scientific management system, and with a systematic approach to solve related problems. The setting of the course is „short yet effective“, and related knowledge can be learnt in just three class sessions.
Training Content
Session I
- Introduction
- Automotive Industry(IATF,VDA,AIAG,Automotive Standard Law,CSR)
- Quality Management System
- ISO 9000
- IAFT 16949
- VDA6.x
- Quality Audit(Quality Management System Audit)VDA6.3 (Process Audit)VDA6.5 (Product Audit)
- MLA (Project Management)
Session II
- Production Process and Product Approval: VDA2& PPAP
- Methods and Tools:
- QFD,FMEA,SPC,VDA5,8D,Poka Yoke
- KVP/Kaizen/Lessons Learned
- Automotive Spice
Session III
- Product Responsibility:
- PSB & PSCR
- Chinese Automotive Recall Law(KBA,NHTSA)
- Automotive Digitalization:
- Future Technology
- Connected Driving(V2V and V2X)NEV
Certificate/Exam
Each online session will be followed by an online examination (multiple-choice questions) based on a document (test form) that will be provided to attendees before the course starts. The test document is password protected and the instructor will provide the password at the end of each learning session. Each test will take part directly after each session and you will have 30 minutes in total for each test. Your answers (file) have to be sent to an Email address after its completion within a certain period on the same day. All three tests of each session are needed in order to finally receive the VDA QMC Driver License certificate. You will receive further instruction after successful registration for each session.
Conditions to receive the VDA QMC Driver License certificate:
1. All above sessions need to be completed
2. Multiple choice session correct rate must be equal to or higher than 70%
As a world leading management consultation and total quality solution provider established in 2003, ACCU is a multinational service group registered in British Cayman Islands with its global operation headquarters located in Suzhou Industrial Park, China. The company owns more than 1000 employees (including more than 400 international employees), more than 600 professional quality technicians, and a team of more than 50 consultants and training experts in its subsidiaries and offices covering 30-odd countries and regions across the globe.
Committed to building a world-leading service platform, ACCU relies on its worldwide quality relay centers and after-sale service centers to provide integrated solutions to multiple industries along the global supply chain of intelligent manufacturing by virtue of its independently developed TQS cloud data platform APP.
ACCU has now become the world’s top consulting company engaged in global business management and quality management, Asia’s largest quality service company for the supply chain of electronics and automotive manufacturing, the first quality management company in China to serve globally-top automobile manufacturers, and the world-leading quality solution provider and successful implementer for the new-energy vehicle and electric automotive industry.
Date: | 14 – 18 March 2022 |
Time: | 9:00 am – 5:00 pm |
Venue: | German Centre Taicang |
Language: | Chinese |
Price: | 25,000 RMB per person (the price includes lunch and coffee break) |
Participants: | max. 15 |
Digital transformation is already revolutionizing every aspect of our lives, changing the way we live, work and play. Throughout this period of uncertainty, TÜV SÜD is striving to add value to governments, businesses and consumers worldwide. The aim is to inspire trust in technology, enabling progress by managing technology-related risks and facilitating change. This commitment is embodied in the claim “Add value. Inspire trust.”
TÜV SÜD Academy is one of the world’s leading providers of technical services related to quality, safety and compliance. The offered training, certification, testing and inspection services are designed to improve the quality of the customers’ products, systems and processes.
Course Introduction
Based on our long-standing practical experience in the field of Functional Safety we supply you with the necessary expertise for the updated ISO 26262 2nd Edition. Safety is one of the key issues in the development and now valid for all road vehicles like Trucks, Buses, Motorcycles and Automobiles. The sector specific needs of electrical and/or electronic (E/E) systems within road vehicles is explained in this standard. Our training modules are based on the practical use of this standard in your daily business to avoid increasing risk from systematic and random hardware failures.
Target Group
Engineers who responsible for product design, R&D, production, maintenance, researching, quality, testing, functional safety in automobile electronic industry.
Training Content
- ISO 26262 background & system structure
- ISO 26262:2018 overview
- Basic concept
- ISO 26262 Functional safety management
- ISO 26262 document structure
- Organization structure & Job responsibilities of development people
- Lifecycle module, definition, technology & measures standardization of ISO 26262 functional safety
- Functional safety management during developing phrase
- Functional safety management after product releasing
- Risk analysis & concept designing phrase
- Project definition
- FMEA & FTA analysis
- ASIL definition & confirmation
- Definition of safety goal and ASIL decomposition
- System designing phrase
- Technical safety proposal development of functional safety
- Technical safety requirements
- Safety requirements output
- Hardware development & evaluation
- System development requirements
- Hardware development process & safety requirements
- Quantitative analysis and qualitative analysis during hardware developing process
- Reliability analysis of hardware
- Define safety measures & hardware fault diagnosis
- Hardware fault category, fault indicators, data calculation of reliability analysis etc.
- Safety evaluation
- Software development & evaluation
- Software development requirements
- Software safety analysis
- Foundamental requirements for software developing process
- V-module
- Software change management
- ISO 26262 & Auto SPICE
Derzeit gibt es keine neuen Seminarangebote. Die Seminarangebote werden in Kürze aktualisiert. Bitte folgend Sie unserem WeChat Account um sofort über neue Seminarangebote informiert zu werden.
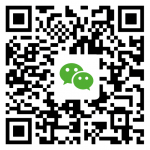
Quicklinks
Kontakt
Dongting Building, 15. Stock
Middle Zhenghe Road 319
215400 Taicang, PR China
Telefon +86 512 5320 3188
Kontaktformular
Anfahrt
Kontakt
Dongting Building, 15. Stock
Middle Zhenghe Road 319
215400 Taicang, PR China
Telefon +86 512 5320 3188
Kontaktformular
Anfahrt
Bleiben Sie auf dem Laufenden über aktuelle Veranstaltungen, Neuigkeiten und interessante Themen rund um das German Centre Taicang.
WeChat: 太仓德国中心
Dongting Building, 15. Stock
Middle Zhenghe Road 319
215400 Taicang, PR China
Telefon +86 512 5320 3188
Kontaktformular
Anfahrt
Impressum | Datenschutz – Konzept & Umsetzung durch INCREON
Impressum | Datenschutz
Konzept & Umsetzung durch INCREON